Unraveling the Power of GRP Housings: A Comprehensive Guide
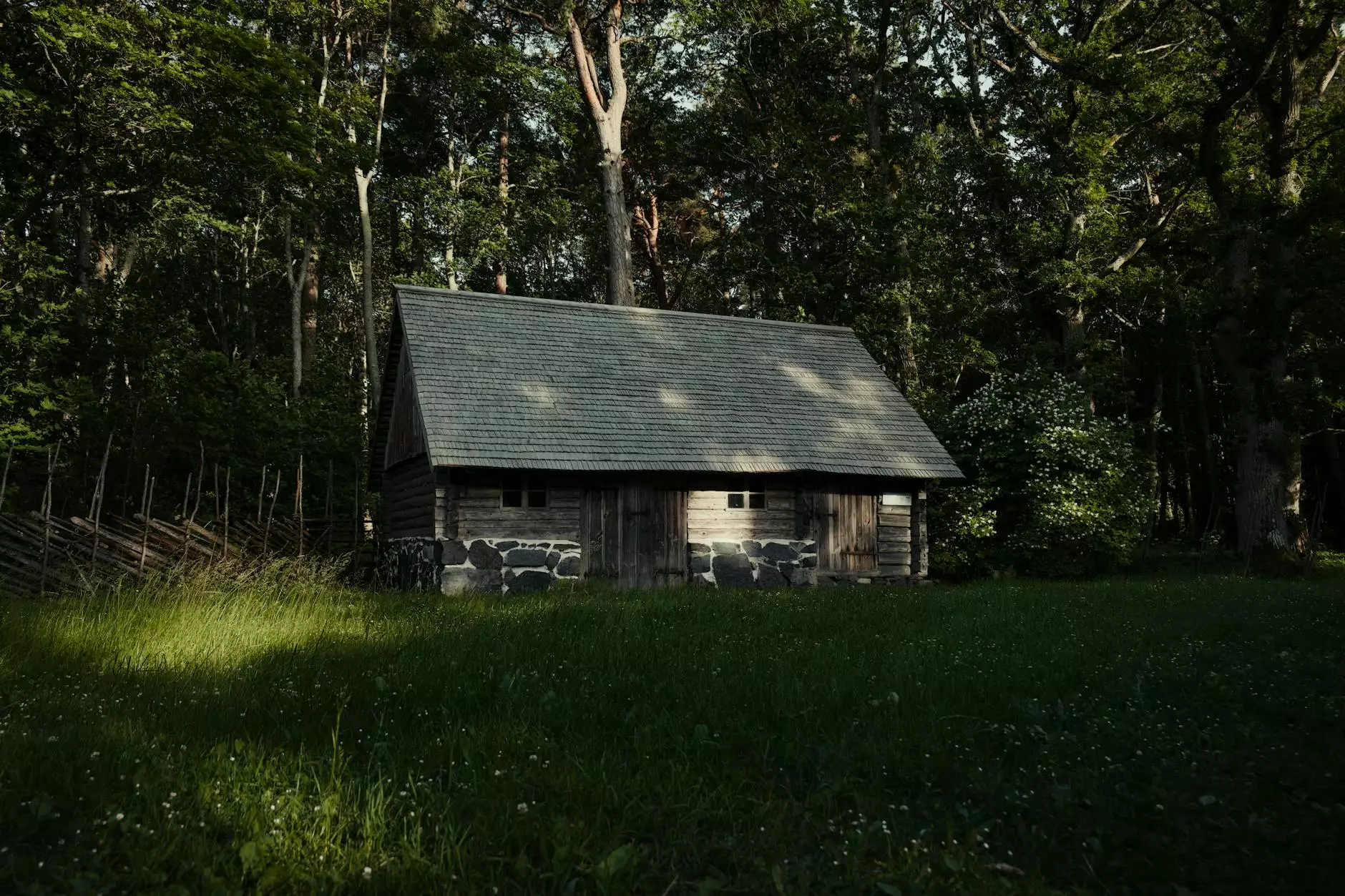
Glass Reinforced Plastic (GRP) housings have become essential components in various industrial applications due to their remarkable strength, lightweight characteristics, and corrosion resistance. This article delves deep into the many facets of GRP housings, exploring their advantages, applications, and the exciting future they hold within different sectors.
What Are GRP Housings?
GRP housings are components made from glass reinforced plastics, a composite material created by embedding strands of glass fibers in a plastic matrix. This synergistic blend results in a product that boasts incredible structural integrity, making it ideal for numerous applications across various industries.
The Composition of GRP: Key Materials and Their Benefits
The beauty of GRP housings lies in their composition. The primary materials involved include:
- Glass Fibers: These provide tensile strength and stiffness to the final product, ensuring durability even in harsh environments.
- Polymer Matrix: This often consists of unsaturated polyester resins, which offer excellent chemical resistance and can be formulated to provide additional properties such as UV stability.
- Additives and Fillers: Depending on the application, various additives can be incorporated to enhance flame resistance, thermal stability, and other performance aspects.
Advantages of Using GRP Housings
There are numerous advantages to selecting GRP housings for your industrial needs:
- Lightweight: Compared to traditional materials like metal, GRP is significantly lighter, which facilitates ease of handling and installation.
- Corrosion Resistance: GRP withstands harsh chemicals and environmental factors, making it suitable for use in diverse settings—from marine to industrial.
- Cost-Effectiveness: While the initial cost may be higher than conventional materials, the reduced maintenance and replacement costs associated with GRP can lead to long-term savings.
- Thermal Insulation: GRP provides excellent thermal insulation, helping regulate temperatures within enclosures and improving energy efficiency.
- Design Flexibility: The manufacturing process of GRP allows for intricate designs, tailoring the housings to specific needs and applications.
Applications of GRP Housings
The versatility of GRP housings permits their use in a myriad of applications, including:
1. Electrical Enclosures
In the electrical industry, GRP housings serve as protective enclosures for sensitive electrical components, ensuring safety and durability in challenging environments.
2. Telecommunications
GRP is widely used for housing telecommunication equipment, offering robust protection against weather elements while being lightweight for easy installation.
3. Automotive Components
Many automotive manufacturers utilize GRP housings for lighter vehicle components, promoting fuel efficiency and performance.
4. Marine Applications
The marine industry benefits from GRP due to its resistance to saltwater corrosion, making it a preferred choice for boat enclosures and equipment housings.
5. Wastewater Treatment
GRP housings are prevalent in wastewater treatment plants, as they resist the aggressive chemicals often present in wastewater, prolonging the lifespan of the structures.
How GRP Housings Are Manufactured
The production of GRP housings typically involves several key steps:
- Material Selection: Choosing the right resin system and glass fiber type based on performance criteria.
- Mould Design: Creating moulds that allow for the desired shape and specifications of the housing.
- Lay-Up Process: Glass fibers are layered and saturated with resin, ensuring thorough coverage and bonding.
- Curing: The mould is heated or left to cure at room temperature, solidifying the material into a strong composite.
- Finishing: Post-curing processes, such as trimming and surface finishing, prepare the final product for installation.
Future Trends: The Evolution of GRP Technology
The future of GRP housings is promising, with ongoing research and development leading to enhanced materials and manufacturing techniques. Some notable trends include:
1. Sustainable Practices
With increasing focus on environmental sustainability, manufacturers are exploring bio-based resins and recycling options for GRP materials.
2. Advanced Applications
The integration of smart technologies, such as IoT devices within GRP housings, is paving the way for smarter infrastructure and monitoring solutions.
3. Customization and 3D Printing
The rise of 3D printing technology has the potential to revolutionize how GRP housings are designed and produced, leading to more tailored solutions for specific needs.
Conclusion: Why GRP Housings are the Future of Industrial Applications
In conclusion, GRP housings represent a perfect blend of strength, durability, and versatility, making them indispensable in various industries. Their growing popularity is attributed to their numerous benefits, including lightweight construction, corrosion resistance, and cost-effectiveness.
As technology progresses, the evolution of GRP and its applications will undoubtedly expand, emphasizing the importance of staying ahead in adopting innovative materials like GRP in future developments. When considering materials for your next project, GRP housings should be at the forefront of your choices, leading the way into a sustainable and efficient future in manufacturing and construction.
For more information on GRP housings and how they can benefit your business, visit Celtic Composites.